The definition ‘digital servo drive’ typically describes a drive unit that can be ‘digitally’ configured. The progression from analogue to digital drive solutions also saw many of these new ‘digital’ drives operate direct from the mains supply. Therefore, particularly for AC servo drives, it may also be assumed that the drive operates ‘direct on-line’, from single- or three- phase mains, without the need for a transformer.
It should be noted that ‘direct on-line’ can have a different meaning, depending on the drives design. Some drives require ancillary components, such as filters or chokes, to meet EMC compliance. Others don’t.
However, digital servo drives can also be low-voltage units operating off a DC supply or batteries.
Digital drives do not have potentiometers, resistors, capacitors, solder bridges, etc. to effect the set-up, but a programmable interface. This might be accessed via an integrated or pluggable keypad, but is predominantly configured over a link to a PC.
The demand signal, most commonly represents a desired velocity, but can also represent a torque or position.
A feedback sensor in the servo motor reports the motor’s actual velocity and position back to the servo drive (closed loop control). The servo drive then compensates for the variation between demanded and actual values.
Servo systems can be very dynamic without sacrificing accuracy. Servo systems are also very energy efficient.
We offer:
- Single and multi-axis servo drive modules
- Digital, direct-on-line servo drives
- Low voltage digital drives for brushless and brushed motors
- Drives with integrated motion tasks and PLC programming functions
- Drive integrated servo motors
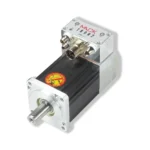
MackTRON2 B60
MackTron2 is the upgrade of the previous version of servo-motor with integrated drive Mack Tron. Power supply 48Vdc, rated torque
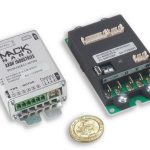
MackNANO miniature servo drive
Axor’s development team have used state of the art electronics, design and engineering techniques to produce an ultra compact drive
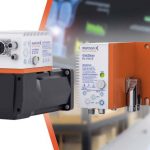
Metronix – smartServo BL 4840-M/D decentralised solutions
To visualise the extreme performance of the smartServo BL 4000-M/D servo drive, we have chosen an example from nature: The
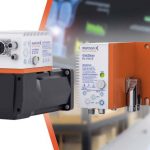
Metronix – smartServo BL 4104-M/D decentralised solutions
Protection High protection class for long-lasting operation in rough environments Thanks to their particularly robust design and excellent manufacturing, the
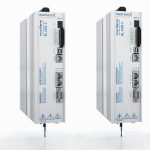
Metronix – smartServo BL 4300C
The SmartServo drive series follows the tradition of Metronix to provide a simple to integrate, user friendly solution to even
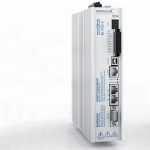
Metronix – smartServo BL 4100C
The SmartServo drive series follows the tradition of Metronix to provide a simple to integrate, user friendly solution to even
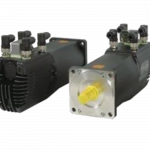
Fast-Back servo motor and drive combo
The Axor FastBack brushless servo motor with integrated drive provides all-in-one, fully digital torque / speed / position control. The
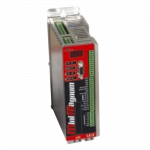
MiniMAGNUM, Digital Servodrive
The fully digital Mini Magnum compact servodrive from Axor Industries measures just 66 wide x 201 high x 141deep (all
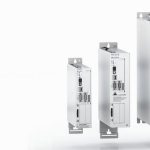
Metronix – ARS 2300 series
The ARS 2000 servo positioning controllers (ARS servo 2nd generation) are intelligent AC servo inverters for operation direct from a
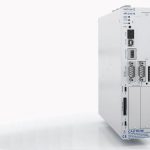
Metronix – ARS 2100 series
The ARS 2100 servo positioning controllers (ARS servo 2nd generation) are intelligent AC servo inverters for operation direct from a
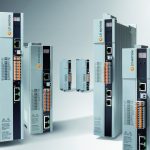
ServoONE junior
This compact, high performance digital servo drive is optimised for the lower power output range, the ServoONE junior range comes
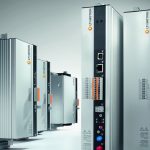
KEBA – Single axis servo drive
The AC-powered ServoOne single-axis servo is suitable for a broad spread of applications thanks to its very wide power output
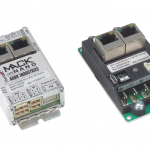
Mack UniNANO
AXOR’s Mack UniNANO (MKUN) builds on the Mack NANO platform and adds drive is an ulta compact, multi-function module for
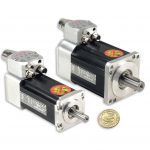
MackTRON Motor Drive Unit
A custom engineered solution to satisfy all demands for quick and simple cabling added to a first-in-class performance to size