Incremental encoders
provide a simple pulse output in relation to the movement of the sensor element across the initiator. In the case of Lenord+Bauer’s magnetic measuring principle the initiator is a fero-magnetic tooth wheel.
Position is derived by the connected electronics, which can be a motion controller, PLC, counter or drive unit, by utilising a reference mark (also referred to as the Zero marker or Z channel) as the starting point. The electronics then track the pulse output from the encoder to establish position.
The Lenord+Bauer magnetic incremental encoders have internal electronics that can derive multiple “pulses” off a single tooth and in this way the encoders offer a resolution of up to 273,408 pulses per shaft revolution (GEL 260 series).
Absolute encoders
provide an ‘actual’ position value, derived from the orientation of the encoder shaft in respect to the sensor element. This is achieved by coding the disc attached to the encoder shaft. The code pattern can be evaluated and so the position is obtained. In the case of Lenord+Bauer’s magnetic measuring principle the initiator is a fero-magnetic disc integrated in the encoder.
Position is output as a ‘value of position’ to a motion controller, PLC, counter or drive unit via a serial link. This is typically an SSI data string or in the form of a fieldbus compatible reference.
The Lenord+Bauer magnetic absolute encoders have internal electronics that can derive up to 16,384 positions per turn (single-turn) of the encoder shaft. In addition an array of magnets, sensed by a set of geared sensor elements, can count up to 4,069 revolutions of the shaft (multi-turn).
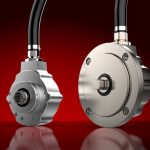
GEL 2701, 2710 and 2712multi-channel rotary encoder
The GEL 2701, 2710 and 2712 multichannel rotary encoders were specially designed for the requirements of the rail vehicle industry.
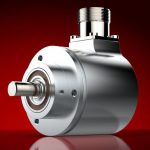
GEL 2037 magnetic absolute encoder
The multiturn absolute rotary encoders in the GEL 2037 series provide an unambiguous position value for each angular position with
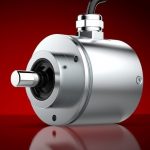
GEL 2010 magnetic incremental encoder
The GEL 2010 encoders contain a contact-less magnetic sensor system and a precision toothed wheel. They have proven themselves in
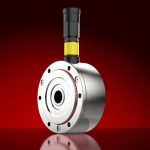
GEL 295x customisedhollow-shaft precision encoder
The precision encoders GEL 295x are designed as a modular, application-specific encoder system and consist of a housing component and
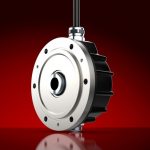
GEL 293 hollow-shaftmagnetic incremental encoder
The magnetic incremental rotary encoders GEL 293 are based on contactless magnetic scanning of an integrated ferromagnetic precision target wheel.
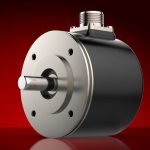
GEL 260 magnetic incremental encoder with current output
The encoders contain a contact-less magnetic sensor system and a precision toothed wheel. The sensor’s magnetic field is modulated by
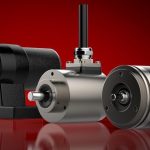
GEL 207, 208, 209 and 219 magnetic incremental encoders
The encoders contain a contact-less magnetic sensor system and a precision toothed wheel. The sensor’s magnetic field is modulated by