VarioCODER Lenord + Bauer’s new rotor position sensor
Efficiency, noise and service life of electric traction motors depend considerably on the signal quality of the sensors used. Our innovative VarioCODER rotor position sensor provides high-precision positions and speeds for ripple-free drive speed and torque control.
The bearing-free, maintenance-free hollow shaft system can be integrated into all motor designs with minimum space requirements. The inductive sensing principle provides highly accurate signals even with large installation tolerances and in environments with stray magnetic fields. This makes it much superior to the very popular resolvers and it can reliably detect rotational speeds of up to 30,000 rpm. This allows drives with maximum torques to be controlled with high quality over the entire speed range.
Efficiency, noise and durability of electric traction motors depend on the control performance. Our operating speed and rotor position
sensors provide you with highly accurate feedback data for drive speed and torque control.
The configurable, inductive rotor position sensor provides stable, offset-free sine and cosine signals corresponding to the number of pole pairs of the synchronous machine. This signal quality is vital for
optimal analog/digital conversion of the controller, as offsets and amplitude errors lead to incorrect quantification and thus incorrect calculation of the angle. This has a direct influence on the drive control accuracy. Its compact design, insensitivity to stray electromagnetic fields, and cost-effective construction and connection technology make it a superior alternative to resolver systems commonly in use today.
Electric vehicle drives are exposed to different load situations during operation. Stop-and-go traffic, rapid acceleration, hitting a curb, or “cruising” at a constant speed with low load place very different demands on the dynamics and quality of the drive control. In all situations, the aim is to avoid torque ripples as far as possible, as these cause detrimental vibrations and noises. At the same time, energy would be wasted, thus reducing the range of battery-powered drive systems.
Synchronous machine structure
a defined magnetic field is
already applied to the motor
rotor. This is usually created
by permanent magnets. Here,
field-oriented control can be
carried out directly with the
rotor angle, since it is equal
to the angle of magnetic flux.
The smaller and more accurately the smallest angular
change can be measured, the
better the field-oriented control can ensure low-vibration
operation.
Typical fields of application:
- Central Motor
- In Wheel Motor
- Twin Motor
- Hydraulic Motor
- Ship Propulsion Systems
- Agricultural and Forestry Systems
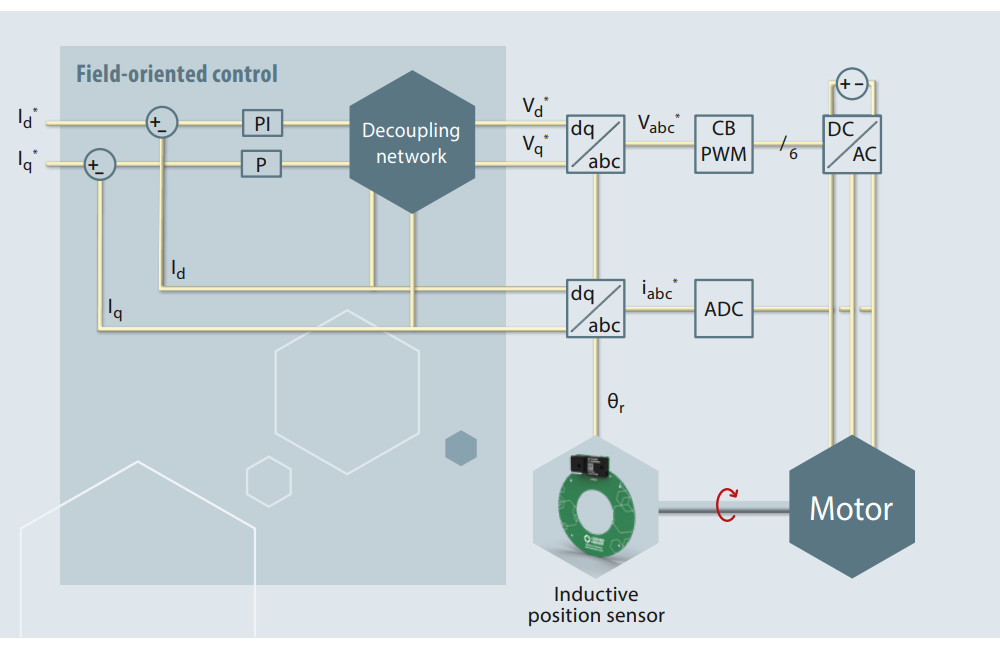