The MACK system is based on a linked, modular design, with no fixed mechanical connection between the modules. All connections are over link-cables. EMC line filter, in-rush and regen circuits are all provided on the MACK POWER module and shared by the connected MACK DRIVE units.
Standard Features
• Several DRIVES powered by one POWER unit
• EMC line filter, in-rush and regen circuits on-board
• USB single cable access for setting and monitoring all drives
• Single, hybrid, cable for motor connection
• Speeder-One software interface
• Optical isolation between power stage and signals
• Operating frequency 8kHz
• Current loop bandwidth 2kHz
• Velocity loop bandwidth 200Hz
• Differential analogue input
• Serial encoder feedback
Options
• Pulse and Direction control mode
• CANbus
• EtherCAT
• Absolute multi-turn encoder feedback
• ComCoder feedback (encoder with commutation tracks)
• Motor holding brake control
• STO Safe Torque Off, safety function
• Extended I/O
• Emmulated Encoder Output
Configurations
• Single-phase 230Vac, 2500W
• 3-phase 230Vac, 4500W
• 3-phase 400Vac, 4500W
Applications
• Several DRIVES powered by one POWER unit
• EMC line filter, in-rush and regen circuits on-board
• USB single cable access for setting and monitoring all drives
• Single, hybrid, cable for motor connection
• Speeder-One software interface
• Optical isolation between power stage and signals
• Operating frequency 8kHz
• Current loop bandwidth 2kHz
• Velocity loop bandwidth 200Hz
• Differential analogue input
• Serial encoder feedback
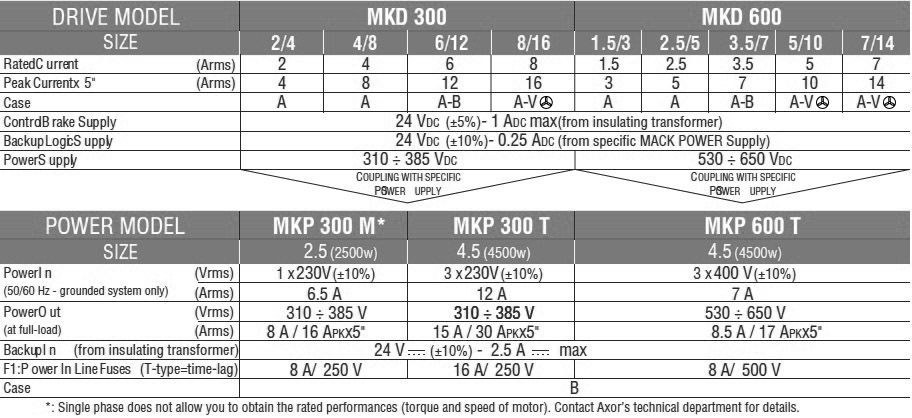