Unlike the MACK DRIVE multi-axis servo drive range, the AXOR’s MACK Indy is designed with low axis count applications in mind.
The drives are designed for a direct-on-line 230Vac, 50/60Hz single phase input and don’t require an expensive 24Vdc power supply for the logic circuit.
The MACK INDY range is complemented by a range of 10 motor variants, in 4 frame sizes, ranging from 0.16 to 5Nm stall torque, with rated speed of 3,000rpm.
The motors feature AXOR’s proprietary MACK serial encoder enabling the connection of motor and drive via a single, hybrid cable.
Standard Features
• In-rush and regen circuits on-board
• Speeder-One software interface with USB for setting and monitoring
• Single, hybrid, cable for motor connection
• Optical isolation between power stage and signals
• Operating frequency 8kHz
• Current loop bandwidth 2kHz
• Velocity loop bandwidth 200Hz
• Pulse/Clock and Direction control mode
• Serial encoder feedback
Options
- EMC line filter
- Differential analogue input
- CANbus
- EtherCAT
- ComCoder feedback (encoder with commutation tracks)
- Absolute multi-turn encoder feedback
- Emmulated Encoder Output
- STO Safe Torque Off, safety function
Configurations
- 1.5, 2.5 and 3.5 Amp versions (with x2 peak current for 5 sec) in 40mm wide housing
- 5 and 8 Amp vesions (with x2 peak current for 5 sec) in 56mm wide housing, with integrated fan
- maximum power output 2.5kW
Applications
• CNC robots
• XY guides
• Healtcare
• Textiles
• Conveyors
• Packaging
• Palletizing
• Carton / box manufacturing
• Printing machines
• Positioners
• Bar feeders
• CNC cutting and milling machines
• Woodworking machines
• Laser and plasma cutting
• Waterjet cutting
• Chemical plants
• Market garden automation
• Welding
• Sharpening
• 3D printers
• Sewing machines
• Upgrade replacement for stepper systems
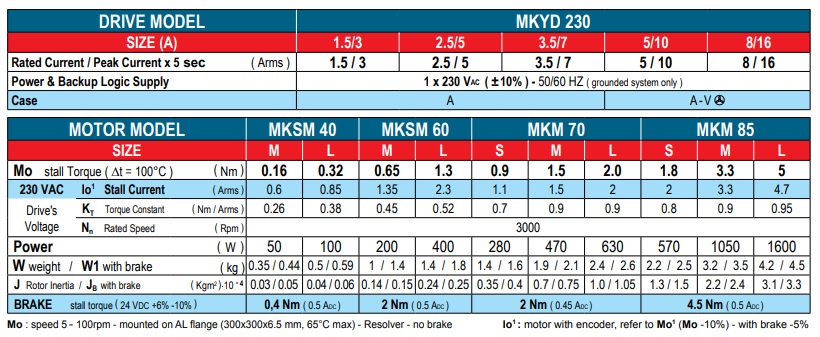